The landscape of manufacturing is undergoing a seismic shift. While challenges like labor shortages, supply chain disruptions, and fluctuating demand persist, a new era of innovation is taking hold. Production of industrial goods surpasses pre-pandemic levels, fueled by a critical transformation: the rise of "smart factories."
This blog delves into the top 10 trends shaping the future of manufacturing in 2024, highlighting the opportunities and strategies for navigating this transformative landscape.
A Story of Resilience and Reinvention
The COVID-19 pandemic exposed vulnerabilities in traditional manufacturing models. However, the industry has not only weathered the storm, but it's also emerging stronger. Production exceeds pre-pandemic levels, and technological advancements propel the industry toward a brighter, more efficient future. This movement, known as Industry 4.0, signifies the next phase in the digitalization of manufacturing.
Industry 4.0: The Power of Automation and Connectivity
At the heart of Industry 4.0 lies a powerful combination of automation, connectivity, and data analytics. Imagine a factory floor where drones deliver parts and streamline inspections or technicians use augmented reality headsets for real-time maintenance. These are not futuristic visions; they represent the transformative potential of Industry 4.0.
Key Trends Shaping the Future of Manufacturing
1. Investing in Technology:
Forward-thinking manufacturers are embracing a new technological arsenal. Robotics, the Industrial Internet of Things (IIoT), and data analytics are revolutionizing production processes.
- Robotics and Automation: Robots are taking on repetitive tasks, improving efficiency and safety while addressing labor shortages.
- Data Analytics: Manufacturers leverage data to gain real-time insights into production processes, optimize machine performance, and predict potential issues.
- Industrial Internet of Things (IIoT): IIoT connects machines and devices on the factory floor, enabling real-time data collection and analysis. This data can be used to optimize production, improve maintenance schedules, and identify areas for improvement.
2. Attracting and Nurturing Talent:
The manufacturing industry faces a critical challenge: a shrinking workforce. To address this, manufacturers are implementing innovative strategies:
- Reskilling Programs: Investing in upskilling and reskilling existing employees equips them with the skills needed to thrive in the digital age of manufacturing.
- Competitive Wages and Benefits: Offering competitive wages and attractive benefits helps manufacturers attract and retain top talent.
- Focus on Work Environment: Creating a positive and engaging work environment is crucial to attracting and retaining skilled workers. This can include promoting safety, offering flexible work arrangements, and fostering a culture of innovation.
3. Sustainability:
A Core Value: Environmental responsibility is no longer a peripheral concern; it's a core value for manufacturers. Here's how they're leading the charge:
- Clean Technologies: Manufacturers invest in clean technologies, such as renewable energy sources and energy-efficient equipment, to reduce their environmental footprint.
- Waste Reduction: Minimizing waste throughout production is a crucial sustainability goal. This can involve using recycled materials, optimizing production processes to reduce scrap, and implementing effective waste management strategies.
- Sustainable Materials: Manufacturers increasingly use sustainable materials in their products, catering to a growing consumer demand for eco-friendly options.
4. Reevaluating the Supply Chain:
The pandemic exposed the
vulnerabilities of globalized supply chains. Manufacturers are taking steps to build resilience:
- Supplier Diversification: Diversifying supplier bases across different regions reduces dependence on single sources and mitigates risks associated with disruptions.
- Digital Supply Chain Tools: Leveraging digital tools for supply chain management provides greater visibility into production processes, inventory levels, and potential disruptions.
- Reshoring: The trend of bringing production back home is gaining traction for specific industries. This can offer greater control over quality and reduce reliance on long-distance transportation.
5. Product as a Service (XaaS):
A novel approach to product ownership is gaining traction: the "Product as a Service" (XaaS) model. Here, manufacturers offer products as a service, with customers paying for usage rather than ownership. This model presents several advantages:
- Recurring Revenue Streams: XaaS provides manufacturers with predictable and long-term revenue streams.
- Customer Usage Data: XaaS models generate valuable data on customer usage patterns, which manufacturers can leverage to improve product design and develop new services.
- Enhanced Customer Experience: XaaS can enhance the customer experience by offering regular maintenance and upgrades, ensuring customers can access the latest technology.
Do You Know
A 2024 forecast by IBISWorld, a market research firm, predicts a surge in US industrial manufacturing revenue within specific segments. Over these five years (2023-2028), solar power equipment is expected to experience the most dramatic growth, with a compound annual growth rate (CAGR) of 25.5%. This is followed closely by 3D printers and drones, both boasting a projected CAGR of 24.1%. Finally, hybrid and electric vehicles are anticipated to increase by 22% annually.
Building the Factory of the Future
The factory of the future will be a marvel of automation and efficiency. Drones will whiz through the air, delivering parts and conducting automated inspections. Robots will handle intricate assembly tasks precisely, while humans oversee the operation, focusing on critical areas requiring creativity, problem-solving, and strategic decision-making. Advanced analytics will provide real-time insights into every facet of production, enabling proactive maintenance and optimized resource allocation.
This vision of the future factory hinges on integrating several key technologies:
- Autonomous Mobile Robots (AMRs): Unlike traditional industrial robots, which are confined to a specific workspace, AMRs navigate freely within the factory environment, performing tasks like transporting materials and conducting inspections.
- Additive Manufacturing (3D Printing): 3D Printing allows for the on-demand creation of complex parts, enabling rapid prototyping and customization, leading to greater flexibility and reduced lead times.
- Artificial Intelligence (AI): AI algorithms can analyze vast amounts of data from sensors and machines, enabling predictive maintenance, optimizing production schedules, and identifying potential quality issues before they occur.
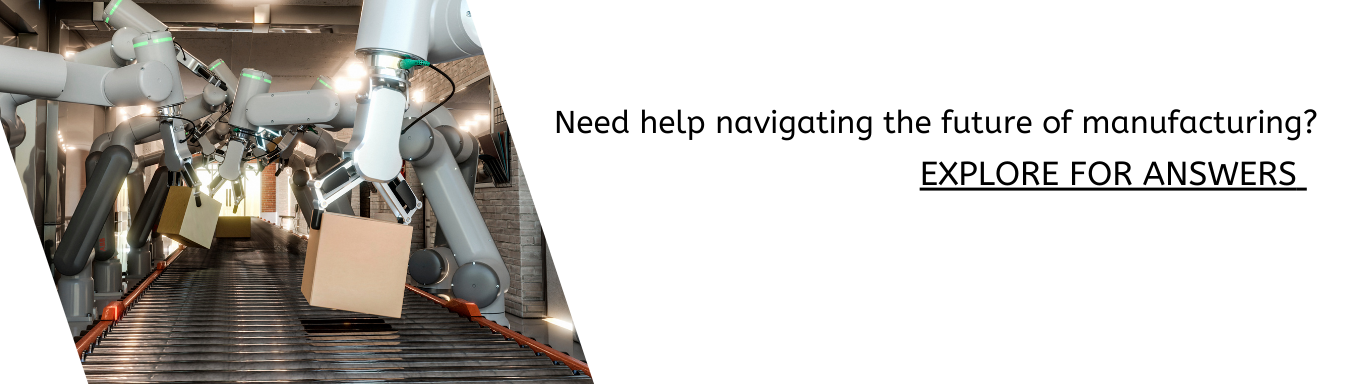
Robots Take Center Stage: A Growing Trend
While some sectors might be experiencing dips in adoption, the overall trend for automation is positive. Robots, cobots (collaborative robots designed for human interaction), drones, and autonomous vehicles are rising.
North American companies are leading the global industrial robot market boom, with a 25% increase in robot orders during Q2 2022. While a temporary slowdown occurred in early 2023, the long-term outlook remains optimistic. Grand View Research anticipates a robust global market with a CAGR of 10.5% between 2023 and 2030.
Cobots, designed explicitly for safe collaboration with humans, are experiencing even more explosive growth. According to ABI Research, the global cobot market, valued at $475 million in 2020, jumped to $600 million in just one year. This trend is expected to continue, with projections suggesting the market will reach $8 billion by 2030.
Click Here to Learn in Detail About Robotic Automation (RPAaas)
Challenges and Considerations
While the future of manufacturing is brimming with possibilities, there are challenges to navigate:
- Security Concerns: As factories become more interconnected, cybersecurity threats become more potent. Implementing robust cybersecurity measures is crucial to protect sensitive data and ensure operational integrity.
- Integration Costs: Adoption of new technologies often comes with significant upfront costs. Manufacturers must carefully evaluate the return on investment (ROI) before embarking on a digital transformation journey.
- Workforce Development: The shift towards automation requires a skilled workforce capable of operating and maintaining complex technological systems. Investing in training programs is essential to ensure a smooth transition.
Embracing the Future of Manufacturing
The future of manufacturing is bright, powered by innovation, and driven by a focus on efficiency, sustainability, and human-machine collaboration. Manufacturers can achieve remarkable advancements by embracing Industry 4.0 technologies, investing in talent, prioritizing sustainability, and building resilient supply chains, propelling their businesses toward long-term success.
Conclusion
The future belongs to those who embrace change, invest in innovation, and build a skilled workforce. This blog has provided a glimpse into the exciting future of manufacturing. As technology continues to evolve rapidly, exciting new possibilities will undoubtedly emerge, shaping the factories of tomorrow.